IATF 16949:2016 Certified

Our
Advance Technology
Profile Projector
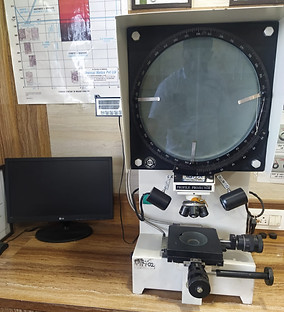
Also known as an optical comparator, or even called a shadowgraph, a profile projector is an optical instrument that can be used for measuring. It is a useful item in a small parts machine shop or production line for the quality control inspection team. The projector magnifies the profile of the specimen, and displays this on the built-in projection screen. On this screen there is typically a grid that can be rotated 360 degrees so the X-Y axis of the screen can be aligned with a straight edge of the machined part to examine or measure. This projection screen displays the profile of the specimen and is magnified for better ease of calculating linear measurements. An edge of the specimen to examine may be lined up with the grid on the screen. From there, simple measurements may be taken for distances to other points. This is being done on a magnified profile of the specimen. It can be simpler as well as reduce errors by measuring on the magnified projection screen of a profile projector.
Mass spectrometer
Mass spectrometry (MS) is an analytical technique that is used to measure the mass-to-charge ratio of ions. The results are presented as a mass spectrum, a plot of intensity as a function of the mass-to-charge ratio. Mass spectrometry is used in many different fields and is applied to pure samples as well as complex mixtures.
These spectra are used to determine the elemental or isotopic signature of a sample, the masses of particles and of molecules, and to elucidate the chemical identity or structure of molecules and other chemical compounds.
In a typical MS procedure, a sample, which may be solid, liquid, or gaseous, is ionized, for example by bombarding it with a beam of electrons. This may cause some of the sample's molecules to break up into positively charged fragments or simply become positively charged without fragmenting. These ions (fragments) are then separated according to their mass-to-charge ratio, for example by accelerating them and subjecting them to an electric or magnetic field: ions of the same mass-to-charge ratio will undergo the same amount of deflection. The ions are detected by a mechanism capable of detecting charged particles, such as an electron multiplier. Results are displayed as spectra of the signal intensity of detected ions as a function of the mass-to-charge ratio.


Micro Vikers Hardness tester
The Vickers hardness test method, also referred to as a microhardness test method, is mostly used for small parts, thin sections, or case depth work.
The Vickers method is based on an optical measurement system. The Microhardness test procedure, ASTM E-384, specifies a range of light loads using a diamond indenter to make an indentation which is measured and converted to a hardness value. It is very useful for testing on a wide type of materials, but test samples must be highly polished to enable measuring the size of the impressions. A square base pyramid shaped diamond is used for testing in the Vickers scale. Typically loads are very light, ranging from 10gm to 1kgf, although "Macro" Vickers loads can range up to 30 kg or more.
Rockwell Hardness Tester
The Rockwell hardness test method, as defined in ASTM E-18, is the most commonly used hardness test method. You should obtain a copy of this standard, read and understand the standard completely before attempting a Rockwell test.
The Rockwell test is generally easier to perform, and more accurate than other types of hardness testing methods. The Rockwell test method is used on all metals, except in condition where the test metal structure or surface conditions would introduce too much variations; where the indentations would be too large for the application; or where the sample size or sample shape prohibits its use.
The Rockwell method measures the permanent depth of indentation produced by a force/load on an indenter. First, a preliminary test force (commonly referred to as preload or minor load) is applied to a sample using a diamond or ball indenter. This preload breaks through the surface to reduce the effects of surface finish. After holding the preliminary test force for a specified dwell time, the baseline depth of indentation is measured.
After the preload, an additional load, call the major load, is added to reach the total required test load. This force is held for a predetermined amount of time (dwell time) to allow for elastic recovery. This major load is then released, returning to the preliminary load. After holding the preliminary test force for a specified dwell time, the final depth of indentation is measured. The Rockwell hardness value is derived from the difference in the baseline and final depth measurements. This distance is converted to a hardness number. The preliminary test force is removed and the indenter is removed from the test specimen.

Microscope

The most common type of microscope (and the first invented) is the optical microscope. This is an optical instrument containing one or more lenses producing an enlarged image of a sample placed in the focal plane. Optical microscopes have refractive glass (occasionally plastic or quartz), to focus light on the eye or on to another light detector. Mirror-based optical microscopes operate in the same manner. Typical magnification of a light microscope, assuming visible range light, is up to 1250x with a theoretical resolution limit of around 0.250 micrometres or 250 nanometres.[20] This limits practical magnification to ~1500x. Specialized techniques (e.g., scanning confocal microscopy, Vertico SMI) may exceed this magnification but the resolution is diffraction limited. The use of shorter wavelengths of light, such as ultraviolet, is one way to improve the spatial resolution of the optical microscope, as are devices such as the near-field scanning optical microscope.